"I am a luthier who builds classical guitars that represent the cutting edge of development in the world today. I use high tech materials and techniques to produce instruments with greatly increased response when compared to traditionally built instruments. My aim is to build guitars which are powerful and balanced, while retaining a rich traditional classical tone. The extra response of my guitars often attracts comments on their ease of playing because the performer does not have to work as hard to produce tone and be heard. A special neck and fingerboard design ensures an easy buzz free action.
Soundboard
"The soundboard is the soul of the guitar and to a large extent is all the difference between a good guitar and a great one. The soundboard of a Redgate guitar is designed to maximize the strength to weight ratio of the materials. To achieve this I use a carbon fibre reinforced lattice bracing and, usually, a cedar top. This style of bracing was originally developed by Greg Smallman and Peter Biffin, and has been adopted by several Luthiers here in Australia. I use my variation of this system, along with my own developments, to produce guitars with the characteristics I desire. Even though most classical guitars are still built using variations of the Torres fan bracing, the lattice system and derivatives on its design, is now being increasingly used by luthiers throughout the world.
|
"The main idea behind my soundboard is to support the pull of the strings in the most efficient way while allowing maximum movement and spring in the top for volume and projection. The lattice bracing has a unique property of deflecting any flex in the soundboard into an opposite curve on a plane of 90 degrees to the original. Put as simply as I can explain, in order for the top to rock back and forwards around the bridge, it has to resist the tendency for the top to flex sympathetically from side to side, and vice versa. This makes the tops very strong but also very light and flexible. Carbon fibre is used on the bracing along with balsa wood because of its extreme strength and little weight. I have found that varying the angle of the bracing can give me different characteristics to suit specific players requirements. The edges of a Redgate guitar soundboard are flexible to allow the low frequencies to match the increased power of the treble. Overall it results in a powerful guitar across the range with warm full bases and crisp singing trebles. The tuning of the soundboard in construction is much more difficult than a conventional guitar due to the increased volume and frequencies in the sound. I tune my guitars for a traditional tone, and an emphasis on separation and clarity in the finished guitar. Typically, although it varies with each guitar, my soundboards are thicker than other lattice braced guitars but thinner than a conventional instrument.
|
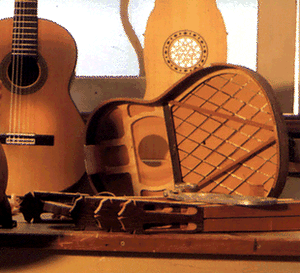 |
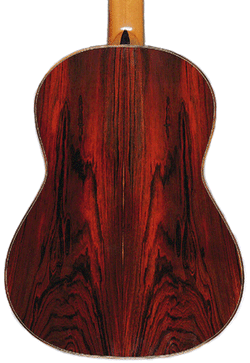 |
The Back and Sides
"In order for a guitar top to fail structurally, the sides of the guitar have to deflect. It follows that stiffening the sides where they meet the top will reduce this deflection and increase the strength of the soundboard. Also this will reduce the leaking of vibrations down the sides and provide a rigid edge against which the top vibrates, much like a speaker cone. The sides of my guitars are much stiffer than a conventional guitar. On some models, I use a wooden ring attached to the sides just below the soundboard but not touching it for even more rigidity. All models have braces running from the end block to the waist, again not touching the top, for added strength. More recently, I have been experimenting with end grain balsa and carbon fibre sandwiches, (much like modern racing boat hull construction), to increase strength even more without adding weight and have had with good results. All of this enables the movement of the soundboard to increase without compromising strength.
|
"The back of my guitars is designed to reflect sound without absorbing or boosting frequencies. The two relatively parallel surfaces of the top and back on a conventional guitar can produce standing waves where the two surfaces can vibrate at the same frequency and cancel out. This leads to unevenness in volume and tone. I use and arched back which has increased strength so does not need bracing. The arching reflects in a superior way and will not allow the formation of standing waves, while the lack of braces allows freer passage of air and sound through the instrument. Overall I have found arched brace-less backs to have better projection and produce an even tone with good voice separation.
|
The Neck
"The neck on any guitar receives half of the vibrating energy of the strings and is often overlooked in the construction of classical guitars. It is vital that the neck be stiff and the frets well seated so that transfer to the neck of string energy is minimized and transferred back to the body of the instrument through conduction. In the past I used to laminate a band of carbon fibre between the fingerboard and the wood of the neck for stiffness and stability but in early 1996 I changed to a truss rod accessible through the sound hole for adjustment. I pre-load the neck slightly before the frets are installed and plane the ebony flat again which gives the neck great stability and stiffness. The truss rod is a two rod system so it does not compress the neck as is the case with most other truss rods, and, in addition to stiffening the neck, allows for fine adjustment for a perfect playing action. The frets on my guitars are pressed in and bedded on epoxy resin. This ensures no air gaps under the frets, resulting in truer sound balance and better sustain. In addition to this, I radius the fret-board for better feel and easier playing.
|
|